Construction sector insolvencies make up almost a third of business fails in Australia.
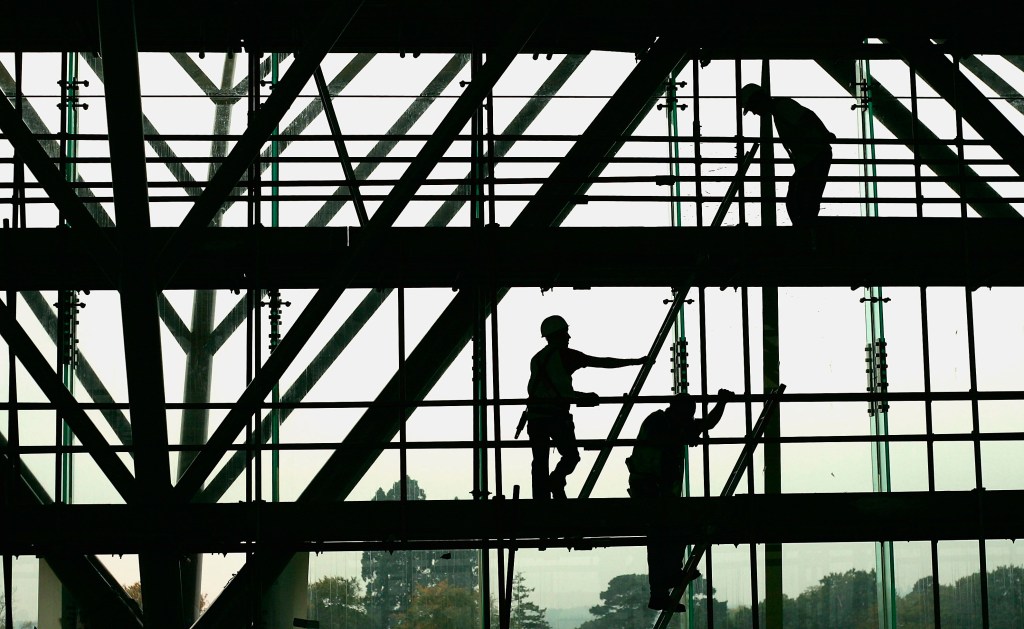
Insolvencies across the construction sector have been steadily increasing since the onset of the Covid-19 pandemic and currently sit at around 29% of total company insolvencies in Australia. Besides Covid-19, a myriad of other factors contributed to this, including supply-chain constraints, high inflationary costs, skill shortages, increasing interest rates and a booming pipeline of government funded infrastructure projects.
While these numerous risk factors impact the financial viability of construction projects, there are mitigating strategies that can be implemented to significantly reduce these risks.
Key to resolving some of these risks is the engagement of a Certified Quantity Surveyor from inception and throughout the life of the project.
Further strategies can include:
Design to a budget, don’t budget to a design
All construction projects work to a budget. Irrespective of the procurement methodology, a budget figure of some sort has been established. Unfortunately, many initial project budgets are not based on current market facts or account for escalation prior to works commencing. Budget setting and construction cost management are core skills for Quantity Surveyors working in this space.
Here, engagement of the Certified Quantity Surveyor at project inception to develop a realistic budget is crucial to ensuring the project has any chance of being viable. For developers, this may include engaging with other consultants such as leasing agents to ascertain future rental returns which may offset construction costs. Some projects only become viable if rental returns are considered, and the developer will need to be sure that any increase in construction costs (whether related to supply and demand or improved sustainability) can be compensated by tenant demand, and subsequently higher rental returns.
Developer risks typically include leasing, funding, certainty of costs, and return on investment. Where a developer has an underlying margin requirement of ~20%, establishing the Certified Quantity Surveyor as key consultant will enhance the ability of achieving that return by ensuring the design reflects all the factors impacting construction cost (time, material supply and carbon emitted).
With increasing interest rates, product costs and supply-chain delays, the cost of construction will also increase. A Certified Quantity Surveyor with experience in these areas will be able to establish a realistic project budget. Even projects with “performance-based” outcomes have a budget to work within.
Tender prices should account for material and labour cost escalation
During the tender period unresolved items often remain, which contractors are required to identify and work through, resulting in Requests for Information (RFI’s) from contractors seeking clarification. This leads to numerous addendums being issued, which is reflective of an inadequate design, scope, planning and risk documentation.
The Australian construction market currently has limited capacity which is being further hampered by a shortage of skilled expertise, of around 105,000 people, in all areas. When the workload exceeds capacity, the results are not in the client’s interest through increased pricing. The real issue is the lack of resources to complete the work, resulting in firms having to pay additional costs to maintain and attract staff, putting pressures on the sector. This in turn impacts cost, time, and quality, which is detrimental to the industry.
At present the overall Australian construction market is relatively stable, however within that market are sub-regions which are displaying varying degrees of volatility. In general terms construction material cost increases peaked in the third quarter of 2022, and is currently easing, however the pass through is taking time to flow through the supply chain. At the same time, mechanical, engineering, plumbing, and fire protection equipment are experiencing price increases.
To mitigate this risk, preplanning and making early payments to lock-in shipping times to get products into the country will help in creating certainty. Facades, structural steel, and mechanical and electrical equipment are all mostly procured overseas. If there is another lockdown or delays globally, this will have flow-on effects for contractors.
Going forward, labour cost increases are likely to be significant in late 2023 when many east coast enterprise bargaining agreements are up for renewal.
Ensure the contract includes Rise & Fall provisions
The high inflationary climate and supply-chain issues have resulted in time and cost impacts on construction projects, which in turn, has led to the collapse of some construction firms. As a consequence, we have seen the re-introduction of rise and fall clauses in construction contracts.
The construction process only allows for minor contingencies to be included in contractors and subcontractors pricing. Recently, COVID-19 lockdowns and wet weather have absorbed a large portion, if not all contingency from the market.
While larger, more sophisticated subcontractors may have the ability to review each project in more detail with detailed take-offs, an understanding of escalation, and foreign exchange, the greater risk is associated with smaller contractors and sub-contractors who do not have the same level of capacity. If there is a sudden movement, these firms may have to step back and remove themselves from the bidding process, leaving those who have relied on their offer holding the shortfall.
While not being the remedy to all construction contract issues, the inclusion of rise and fall clauses with an independent verifiable check mechanism offers a win-win solution for contractors and principals alike. In this area, governments and government agencies are best positioned to lead the change to achieve an equitable outcome in circumstances where certainty of supply and cost of construction labour and materials cannot be achieved.
Here, the Certified Quantity Surveyor has an important role to play in independently verifying project budgets. They can also make any adjustments to the cost of installed construction components brought about by supply and/or costs issues which were outside the contractor’s ability to either lock in, or were forced upon them, due to contributing factors which were outside its control.
Utilise a two-stage contract with early contractor involvement whenever possible
Early engagement by clients with contractors is critical to ensure base assumptions are correct and if not, adjust the design or parameters early to make sure the project can work. This could mean changing a product, accelerating the project, or delaying it.
In addition, both clients and contractors should opt for a two-stage contract, which provides greater cost certainty, potentially leading to cost savings for the client and reduced risk of delays.
Two stage contracts are often used to enable the early appointment of a contractor, prior to the completion of all the tender information, that they would require to be able to offer the client a fixed price. In the first stage a limited appointment is agreed allowing the contractor to begin work and in the second stage a fixed price is negotiated for the contract.
Two-stage tendering can allow a project to progress before the design is complete. Early involvement of the contractor (or other suppliers) should also improve the buildability and cost-certainty of the design, as well as creating a better integrated project team and reducing the likelihood of disputes.
Engage a Certified Quantity Surveyor from project inception
To truly minimise construction project risks, clients should engage the services of a Certified Quantity Surveyor to provide full cost management services.
This requires a Certified Quantity Surveyor with a broad range of professional skills and experience, including an understanding of:
- experience with similar projects and contracts.
- the level of design and identification of deficiencies in documentation.
- all risks associated with the project, i.e., latent conditions, constructability, procurement, and escalation.
- a consistent approach to work breakdown structure and associated cost breakdown structure and format of cost estimate.
- validation through benchmarking of design, pricing and production metrics.
- qualifications, assumptions and exclusions to provide a complete budgetary approach and align pricing during the project’s development at and reconciliation with contractors.
Grant Warner is Chief Executive Officer at the Australian Institute of Quantity Surveyors.