Revolutionising the common electrolyser, Australian start-up Hysata is tackling industries that have been difficult to decarbonise and electrify, like steel and heavy transportation. CEO Paul Barrett reveals the company raised more than $42 million in 2022 and has over $5 billion in conditional orders – all slated for delivery in the second half of the decade.
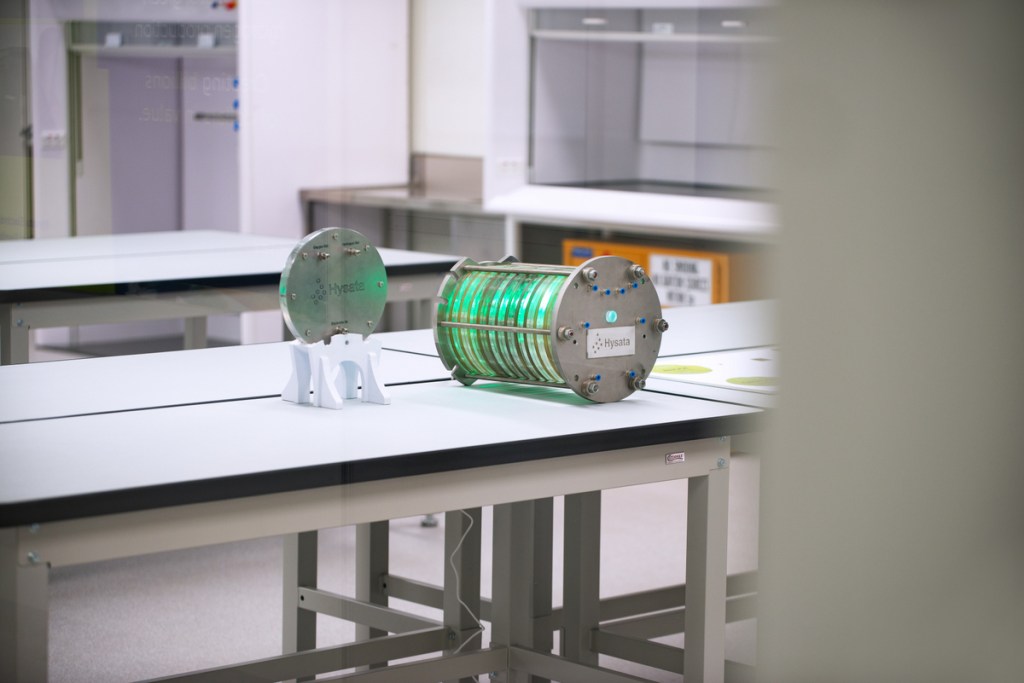
The electrolyser is a common apparatus; it uses electricity to split water into hydrogen and oxygen in a process called electrolysis. But there’s always been a slight problem.
“The challenge is, [electrolysis] consumes a lot of energy because the resistance is high,” Paul Barrett, the CEO of Hysata, says.
Despite being around since the 1800s, electrolysers haven’t seen much improvement. Until about a year ago, the status quo for commercial electrolysers was that a kilogram of hydrogen holds about 39.2 kWh of energy and typically costs about 52.5 kWh of energy to produce. In other words, more energy is required to produce hydrogen than it can provide.
A new start-up, however, out of Port Kembla, south of Sydney, Hysata, says it’s developed the world’s most efficient electrolyser, with 95% efficiency at 41.5 kWh per kilogram of hydrogen. That’s 20% above incumbent technologies, verified in the science journal Nature Communications in 2022.
“What Hysata did was simple and elegant,” Barrett says. “Every electrolyser has a membrane, which is a barrier to stop the mixing of gases [hydrogen and oxygen]. And that’s usually the source of resistance. But we’ve reimagined what that membrane needs to be – and ours is a sponge.”
Twice the thickness of a human hair, Hysata’s membrane eliminates most resistance in the electrolyser. It’s also plastic, which lends itself well to scale. In 2022, the company revealed it raised a $42.5 million Series A round led by Virescent Ventures.
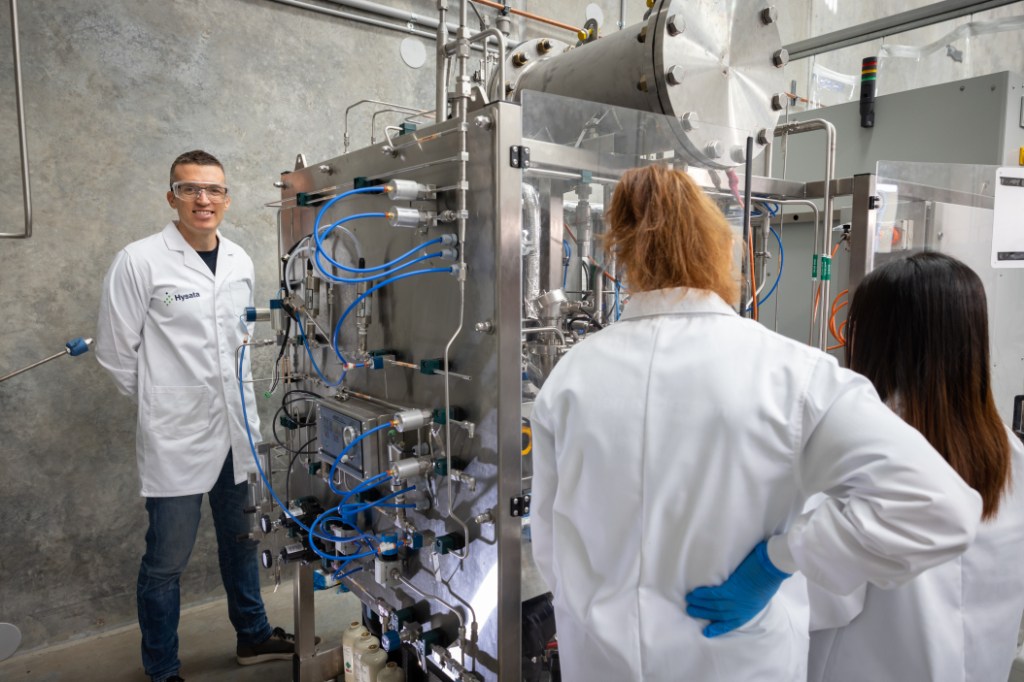
“Hysata has developed the world’s most efficient hydrogen electrolyser in practice,” Blair Pritchard, partner at Virescent Ventures, says. “This incredible technological advantage gives Hysata a great shot at being a world leader in its field. Hysata also has a great culture of high-quality engineering, a track record of hitting milestones, and was designed for bankability from day one. This means the balance of plant setup will be simpler than anything the world has seen.”
Hysata’s advisory board includes former Australian chief scientist Dr Alan Finkel, former UK Minister of State for Energy and Clean Growth Claire O’Neill, clean energy commentator Michael Liebreich and former BHP boss Dean Dalla Valle (who is its Chair). The Australian Minister for Climate Change and Energy, Chris Bowen, also opened the company’s first electrolyser manufacturing facility and global headquarters in Port Kembla
in August.
“We not only have this game-changing technology, we’ve also got an approach to mass manufacturing and a transformational supply chain. We can hyper-scale manufacturing in a very capital-efficient way. We can get a high throughput of product output with little capital equipment required. That’s what has us, and our customers, excited.”
The technology was developed at the University of Wollongong from a group run by Gerry Swiegers, the chief technology officer at Hysata. “He’s a prolific inventor – and he’s got a real industrial edge to his academic approach,” Barrett says of Swiegers.
As Barrett recounts it, Swiegers sat down with his academic group about five years ago and sought to understand why electrolysers were electrically inefficient. And he invented a new class of electrolyser in doing so.
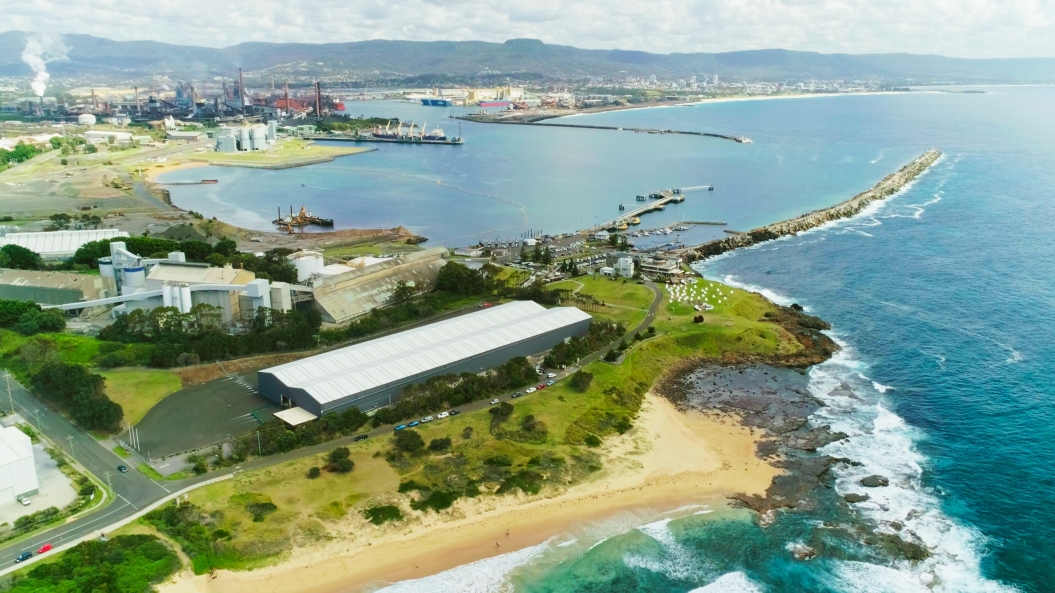
“It’s a game-changing invention,” Barrett says. This electrolyser could, he says, be used to generate green hydrogen (hydrogen produced by renewables) to power companies in hard-to-electrify sectors, helping them achieve net-zero emissions.
“On the path to net-zero 2050, we must electrify everything: the home, factories, heating, cooling, passenger transportation. Once you’ve electrified those, you leave behind the hard-to-abate sectors, which are about 20% of the world’s emissions,”
Barrett says, like steel, chemicals and heavy machinery.
“Right now, about 100 to 150 million tonnes of hydrogen are used today in chemical manufacturing, for fertiliser, for ammonia. We’ll need somewhere between 200-500 million tonnes of green hydrogen to get to net zero. The strategy is to go after those existing users. The opportunity is ginormous.”
Look back on the week that was with hand-picked articles from Australia and around the world. Sign up to the Forbes Australia newsletter here or become a member here.